Smink Group’s Ion Mobility Spectrometry (IMS) system represents a breakthrough in real-time impurity detection for high-purity environments. Designed to meet the rigorous demands of industries such as pharmaceuticals, semiconductors, and biotechnology, the IMS system provides precise, in-line measurement of gas purity levels.
Read moreIn the dynamic semiconductor industry, the soaring demand for ever smaller, more powerful and more complex devices requires rapid product development cycles. Challenges in your supply chain include the need for rapid development, fabrication and validation of crucial high-purity systems.
At Smink Group, we support the constant revolutionary changes in your manufacturing equipment. We design, produce and validate high-purity systems geared to the conditioning and optimised performance of your machines. And we offer unrivalled efficiency and flexibility in driving volume changes during your manufacturing process.
Whether we supply weld assemblies, gas panels, gas or fluid conditioning modules or skids, we ensure zero defects while optimising efficiency. Vacuum pipe systems, distribution infrastructures for bulk gases, nitrogen stretch and leak integrity testing, and total organic carbon measurements are part and parcel of our comprehensive solutions.
Smink Group is certified in accordance with ISO9001:2008 and the SCC (SHE Checked Contractor) safety standards. In addition, we secure ultra-cleanliness in our grade 2 and 4 clean rooms.
Real-time impurity measurement system
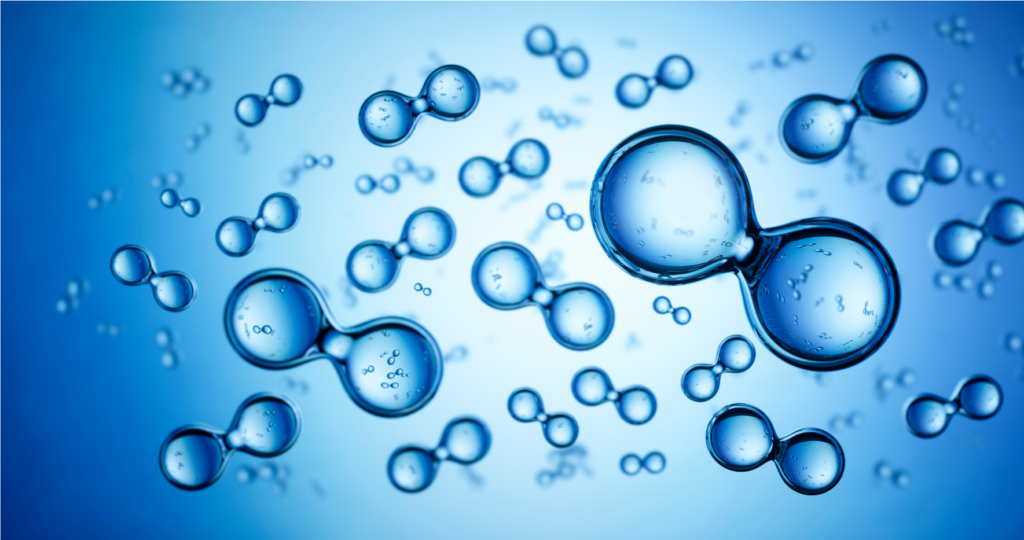
Welding
High-purity gas and fluid tubing systems are at the heart of high-tech manufacturing facilities. Ultra-cleanliness, smoothness and, of course, leak integrity are crucial, when welding these systems. Our highly skilled and qualified welders secure the highest standards in orbital and manual welding.
Read more
CNC tube bending
Compact, ultrahigh-precision tubing built under clean room conditions is crucial to the high-tech industry. In the semiconductor industry in particular, space is limited, resulting in increasingly complex tube forms. To tackle these challenges, we don’t just build to print. Our engineers increasingly take on the entire product development cycle.
Read more